Comme dans d'autres domaines d'application, un outil dédié au management de l'énergie accélère la performance d'une organisation si elle s'appuie également sur des ressources et des méthodes.
Voici donc nos 10 commandements du Lean Management/Kaizen applicables au quotidien par un responsable Energétique visant l'amélioration continue de la performance énergétique de son site industriel. Nous les avons illustrés avec des exemples vécus au quotidien par nos clients, pour vous donner une mise en oeuvre concrète de la boucle PDCA (Plan > Do > Check > Act) appliquée à la norme ISO 50001 sur les Systèmes de Management de l'Energie :
-
- Se débarrasser des suppositions et des status quo historiques. Vos interlocuteurs vous expliquent qu'ils ont toujours procédé de la même façon depuis plusieurs années pour régler une température de consigne ou le démarrage des machines lors de leur prise de poste ? Il y a sûrement des économies qui se cachent derrière cet état de fait dont plus personne ne connaît probablement l'origine.
- Appliquer la règle des 5 pourquoi pour comprendre la racine d'une pratique. Corollaire du point précédent, cette méthode qui consiste à investiguer 5 fois de suite l'origine d'un état de fait, permet d'aller vraiment au fond du raisonnement et de formaliser une pratique pour la faire évoluer si nécessaire.
- Ne pas chercher de coupables mais se concentrer sur des solutions : chaque problème est une opportunité ! Personne ne souhaite être identifié comme responsable d'un gaspillage. Il faut donc être constructif en se concentrant sur la résolution du problème et les économies d'énergie qui peuvent en résulter
- Ne pas chercher à être parfait demain, mais commencer à progresser tout de suite dans l'action. Un exemple concret : un CEE pour financer un variateur de vitesse régulera mieux la fourniture d'air comprimé depuis la chaufferie, mais l'équipe de production d'un atelier peut déjà réfléchir aux moyens de réduire leurs besoins en air comprimé dans l'atelier en attendant son installation.
- Partager les bonnes pratiques plutôt qu'être seul à tout savoir, car personne n'est irremplaçable. L'absence ou le départ d'un collaborateur vers un autre site industriel du Groupe ne doit pas faire disparaître les procédures de maintenance ou d'opérations pratiquées sur le site.
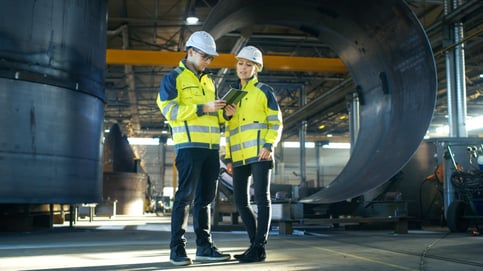
- Chercher des solutions à l'extérieur plutôt que de rester dans l'impasse. L'amélioration continue vient souvent de la sérendipité, le fait de trouver de nouvelles idées à la suite d'un concours de circonstances inattendu, souvent dans le cadre d'une recherche concernant un autre sujet. Pourquoi ne pas échanger avec le responsable Energie du site industriel voisin concernant un problème où l'on a atteint ses limites ?
- Il n'y a pas de question idiote et la parole des autres compte. L'arrivée d'un nouveau collaborateur sur un site peut être une excellente opportunité pour avoir un regard neuf et extérieur sur le quotidien du management de l'énergie.
- Être ouvert au changement avec une attitude positive sans opposition silencieuse. Réduire par exemple le débit d'un réseau d'air comprimé ne signifie pas remettre en cause la compétence d'un opérateur de maintenance. Il s'agit au contraire de valoriser son savoir-faire et mettre son expertise à contribution pour améliorer la performance et la compétitivité de l'entreprise.
- Privilégier la créativité avec l'existant plutôt que d'attendre les investissements. Un équipement ou un site industriel est rarement remplacé ou reconstruit intégralement, et les temps de retour sur investissement ne peuvent en général pas excéder 1 an en raison du contexte économique actuel. Pourquoi ne pas essayer à la place de reproduire le plus souvent possible les conditions de la meilleure performance jamais atteinte par une machine existante ?
- On peut TOUJOURS s'améliorer ! Même si les économies sont moins nombreuses et plus dures à réaliser au fur et à mesure où elles sont mises en oeuvre, elles ne sont souvent bridées que par la créativité et l'envie.
Qu'attendez-vous pour vous lancer ?