As in other fields of application, a tool dedicated to energy management accelerates the performance of an organization if it is also supported by resources and methods.
Here are our 10 commandments of Lean Management/Kaizen applicable to the daily life of an Energy Manager aiming at the continuous improvement of the energy performance of his industrial site. We have illustrated them with examples experienced daily by our customers, to give you a concrete implementation of the PDCA loop (Plan > Do > Check > Act) applied to the ISO 50001 standard on Energy Management Systems:
-
- Get rid of assumptions and historical status quo. Get rid of assumptions and historical status quo. Do your interlocutors explain that they have always proceeded this way for several years to set a temperature or to start the machines when they take their shift? There might be some savings behind this state of affairs, which probably no one knows about anymore.
- Apply the 5 Whys rule to understand the origin of a practice. As a consequence of the previous point, this method, which consists in investigating 5 times in a row the origin of a state of affairs, allows us to really get to the bottom of the reasoning and to formalize a practice in order to make it evolve if necessary.
- Do not look for blame but focus on solutions. Each problem is an opportunity! No one wants to be identified as responsible for a waste. So be constructive and focus on solving the problem and saving energy.
- Don't try to be perfect tomorrow, but start making progress today. A concrete example: an white certificate to finance a variable speed drive will better regulate the supply of compressed air from the boiler room, but the production team of a workshop can already think of ways to reduce their compressed air needs in the workshop while waiting for its installation.
- Sharing good practices rather than being the only one to know everything, because no one is irreplaceable. The absence or departure of an employee to another industrial site of the group must not lead to the loss of maintenance procedures or operations performed on the site.
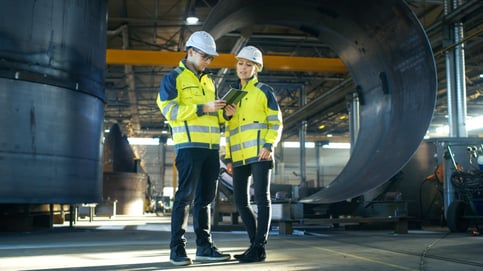
- Look for solutions externally rather than staying stuck. Continuous improvement often comes from serendipity, the fact of finding new ideas as a result of unexpected circumstances, often in the context of research on another subject. Why not talk to the energy manager of the neighboring industrial site about a problem where you have reached your limits?
- There is no silly question, and everyone else's opinion matters. The arrival of a new employee at a site can be an excellent opportunity to get a fresh, outside look at the day-to-day business of energy management.
- Be open to change with a positive attitude without quiet opposition. Reducing the flow of a compressed air network, for example, does not mean questioning the competence of a maintenance operator. On the contrary, it is a matter of valuing his knowledge and putting his expertise to work to improve the company's performance and competitiveness.
- Focus on creativity with existing equipment rather than waiting for investments. A piece of equipment or an industrial site is rarely replaced or rebuilt completely, and the return on investment time cannot generally exceed 1 year due to the current economic context. Why not try instead to reproduce as often as possible the best performance conditions ever achieved by an existing machine?
- There is ALWAYS time for improvement! Even though savings are fewer and harder to achieve as they are implemented, they are often only hindered by creativity and desire.
What are you waiting for to get started?